How to Avoid Peeling Issues in DTF Prints
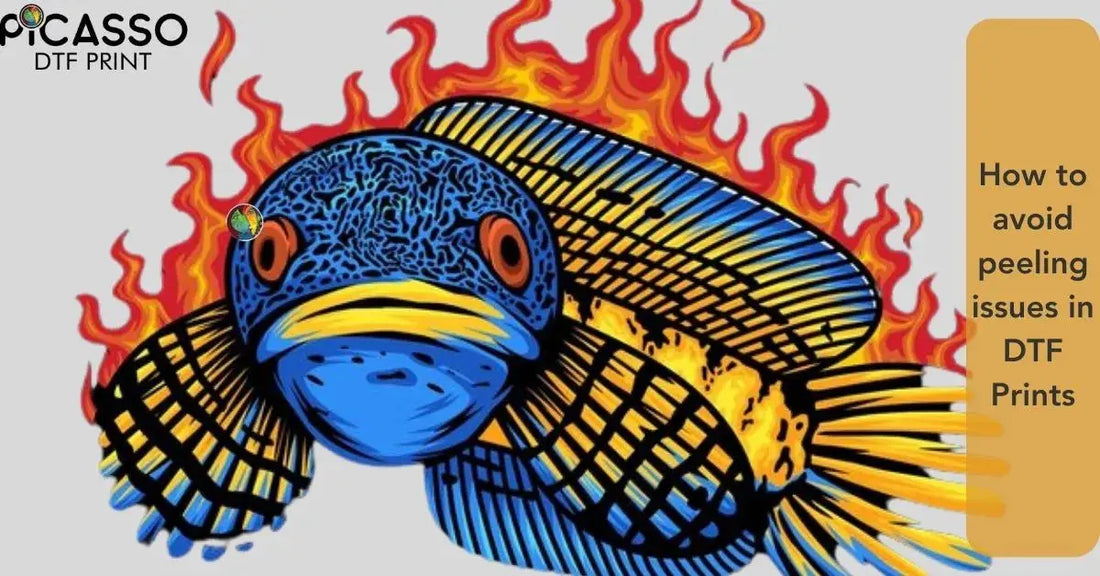
With its bright colors and versatility, Direct-to-Film (DTF) printing revolutionizes garment printing entirely. One thing many users experience related to DTF is peeling, where the design begins to lift off the fabric. This affects the quality and longevity of your prints, but thankfully, it is preventable. In this guide, we will look at the causes of peeling, practical tips for avoiding it, and solutions to ensure your prints look great every time.
What Causes Peeling in DTF Prints?
Prevention of peeling, which is the primary consideration for ensuring the longevity of DTF prints, is determined by understanding the root causes of peeling. You can realize the initialization of the underlying problems to make corrective changes during the printing process and obtain good quality. Some common causes for peeling are improper adhesive application, bad heat press settings, and using contrary fabrics. Also, improper curing or insufficient storage of materials can lead to the same end. Addressing these causes will help avoid peeling and aid the longevity of your designs.
- Low-Quality Adhesives
- Incorrect Heat Application
- Unsuitable Fabrics
- Inadequate Curing
- Improper Storage of Materials
Ā
Low-Quality Adhesives
DTF printing relies on adhesive powder to allow designs to adhere correctly to the fabric. The adhesive's quality and application determine the longevity of the final print. Inferior adhesives or uneven applications can weaken the bond, resulting in peeling and wear. Thus, mixing and applying high-quality adhesive powder to the design is crucial to achieving a long-lasting result.
Incorrect Heat Application
Underheating or not applying enough pressure could result in incomplete adhesive activation, failing to bond the design to the fabric properly. If heat is unevenly applied or pressure is insufficient, the adhesive powder may not be thoroughly melted, and the adhesion may weaken. This will eventually lead to the design lifting off the fabric due to wash or handling. Ensuring that the proper heat and pressure settings are set to produce long-lasting prints is essential.
Unsuitable Fabrics
Some fabrics, such as water-repellents or stretchy synthetics, may not work well for DTF printing because they are not conducive to bonding with the adhesive. These fabrics challenge proper adhesion, which may lead to possible peeling or lifting of your design. Choosing suitable fabrics for DTF printing is essential for a strong long-term bond.
Inadequate Curing
Curing the adhesive powder, a step overlooked by many in the DTF process is essential for the longevity of the design. If not appropriately cured, the adhesive will not adhere well to the fabrics, resulting in a short lifespan of such prints.
Improper Storage of Materials
Should transfer films and adhesives be exposed to excessive moisture or heat during storage, their quality may be severely impaired, rendering them almost useless. Proper storage in a cool and dry environment is vital to preserve the materials for their best performance during printing.
How to Prevent Peeling in DTF Prints
DTF prints require high-quality materials such as adhesive powder, transfer film, and ink to keep the peel away. Ensure the heat press matches the recommended temperature, pressure, and time for the fabric in question to establish a strong bond between the printed image and the substrate. Apply adhesive powder evenly and cure thoroughly for lasting adhesion. Always pre-press the fabric to remove moisture and wrinkles before printing. Last but not least, wash testing should ensure that after various washes, the design will remain intact and look as good as ever.
Ā
1. Use High-Quality Materials
2. Optimize Heat Press Settings
3. Prepare Fabrics Before Printing
4. Apply Adhesive Powder Evenly
5. Master the Curing Process
6. Allow Time for Cooling
7. Perform Quality Control
Ā
Use High-Quality Materials
Invest in premium transfer films, adhesives, and inks. While they may cost more upfront, they offer better durability and reduce rework due to peeling issues.
Optimize Heat Press Settings
Follow the recommended settings for temperature, pressure, and time. These settings can vary depending on the fabric type and design size. Testing a small sample before full production can save time and effort.
Prepare Fabrics Before Printing
To allow for optimum adhesion, specific requirements must be fulfilled before the printing activity on the fabrics, such as cleanliness, dryness, and no wrinkles on the fabric surface. Press the garment for a few seconds to remove any oil or moisture that could affect the transfer process. This step helps ensure smooth, even design application and improves print quality and durability.
Apply Adhesive Powder Evenly
Ensure the adhesive powder is spread evenly over the design and shake off any excess. Uneven application can lead to weak spots that are prone to peeling.
Master the Curing Process
Curing the adhesive powder thoroughly is essential to achieve a strong, lasting bond between the design and the fabric. Whether using a curing oven or a heat press, applying consistent heat across the entire design is crucial to ensure the adhesive melts evenly. Uneven curing can lead to weak adhesion and potential peeling over time. Taking the time to ensure proper curing helps ensure the design remains intact, even after washing or extensive use, for a durable and professional finish.
Allow Time for Cooling
After transferring the design, let it cool completely before peeling off the transfer film. Rushing this step can weaken the bond and cause lifting.
Perform Quality Control
Always wash a sample of your design to check it before bulk production, which is a great way to intercept pre-production problems. It also puts the design to the durability test after untold washes. With this test performed, weak points, such as poor adhesive strength and colour run ability, can be easily detected. Taking preventative measures assures that your prints are up to the standards set by your customers and produce a quality and long-lasting result.
Tips for Better DTF Printing Results
For optimum DTF printing results, proper maintenance and calibration should be performed regularly on the machine to keep its performance consistent. A Teflon sheet helps ensure even heat distribution and protects the fabric during pressing. Always test a sample before production to fine-tune the settings and avoid potential troubles.
- Maintain Your Equipment: Regularly cleaning and calibrating your heat press system is essential to operate with consistent temperature and pressure continuously.
- Store Materials Properly: Keep transfer films and adhesive powders in a cool, dry place to preserve quality.
- Use a Teflon Sheet: This can help distribute heat evenly and protect the fabric during pressing.
- Test Before Production: Always test on a sample fabric to adjust settings and avoid surprises during bulk printing.
Ā
Conclusion
The peeling problem in DTF printing can be very tricky if tackled incorrectly. However, any peeling problems that do arise can easily be avoided by following some simple techniques. Suitable materials, exact heat press settings, and proper curing are the keys to getting bright and durable prints. At Picasso DTF Printing Services, we proudly provide world-class printing solutions.
Our expertise and commitment to quality ensure your designs come to life for personal projects or business needs. You can trust us to deliver exceptional, vibrant, durable prints that exceed your expectations. Let's create something extraordinary together.
Ā
Frequently Asked Questions
Ā
What should I do if my DTF print starts peeling?
If peeling occurs, you can try reapplying heat and pressure to the affected area. However, prevention is always betterāensure proper heat settings and use high-quality materials.
Can I use DTF printing on any fabric?
DTF works best on cotton, polyester, and blends. Avoid fabrics with coatings or high elasticity, as they may not bond well with the adhesive.
Why does my print peel after washing?
This often happens due to insufficient curing or incorrect heat press settings during transfer. Always follow recommended procedures and perform wash tests.
Is curing necessary in DTF printing?
Curing is essential to activate the adhesive powder and ensure it bonds properly with the fabric. Skipping this step increases the risk of peeling.
How do I store my DTF materials?
To maintain their quality, store adhesive powders and transfer films in a cool, dry place away from moisture and direct sunlight.
0 comments