The Most Common DTF Transfer Errors and How to Fix Them
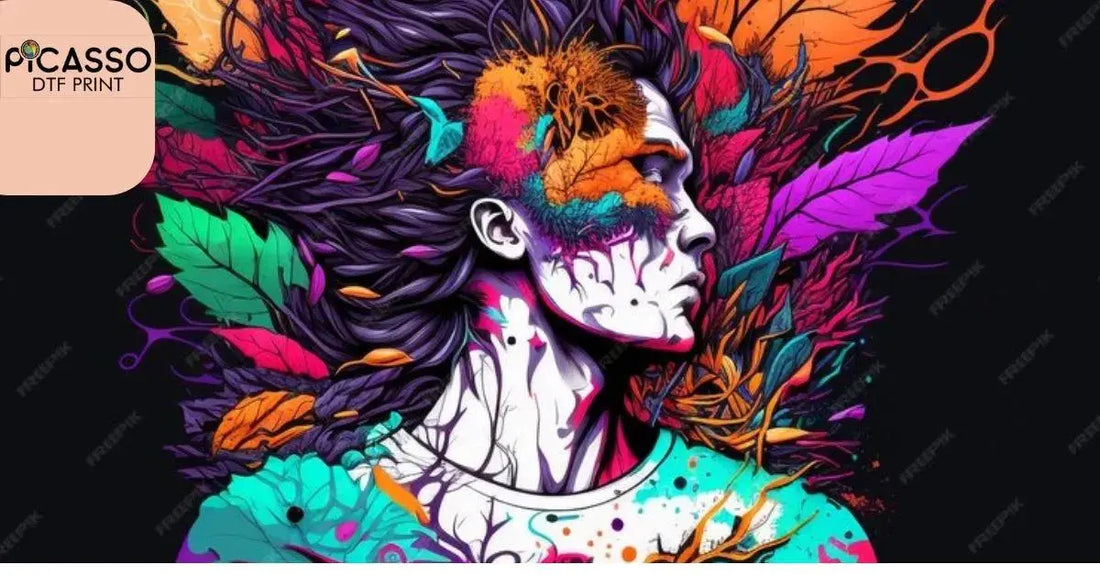
DTF printing is widely used to transfer paper bonded to textiles, plastic, or even ceramics. Although DTF printing has numerous benefits, it tends to err often during transfer. In this blog, we will explain some of the most common kinds of DTF transfer errors along with practical remedies to achieve perfect flawlessness.
Understanding DTF Transfer Errors
Before getting into actual error fixes, there are a few familiar sources of DTF transfer errors that have to be identified:
Incorrect Transfer Temperature: The first source is transfer temperature, which, if set at the proper temperature, would ensure full and smooth transfers.Insufficient Pressure: More pressure is applied while transferring, which leads to an image being poorly attached and not completely transferred.
Inadequate Pre-Press Time: Lack of pre-press time before transferring may prevent the ink from drying completely, causing smudges or bleeding.
Incorrect Transfer Time: A transfer time that is too short or too long will negatively affect the quality of the transfer.
Poor Ink Quality: Low-quality ink may lead to faded colors, poor adhesion, and other problems in the transfer.
Suboptimal Substrate Preparation: Poor substrate preparation can affect the adhesion and appearance of the transfer.
Common DTF Transfer Errors and Solutions
Learn the most common mistakes with DTF printing and how to overcome them. Picasso DTF Print, one of the USA's leading DTF printing companies, shares valuable insight into getting it right.
- Poor Ink Adhesion
- White Ink Issues
- Color Mismatch
- Cracking and Peeling
- Image Distortion
- Uneven Application of Powder
- Ink Bleeding     Â
1. Poor Ink Adhesion
Problem: Inks do not stick very well to the textile, so you encounter all the above-mentioned peeling, cracking, or even fading. Sometimes, this might happen due to a lack of binding the ink into the fibers on the cloth, so over time, it peels away from them—especially with every subsequent washing or with a strong friction impact.
Causes:
Insufficient Powder Application: Application of Low Quantity Powder Leads to Excess Ink Adhesion.
Incorrect curing temperature or time: This affects bonding due to the wrong heat settings.
Lousy quality ink or powder: This weakens adhesions due to low-quality material.Incorrect fabric preparation: Sometimes, poorly prepared fabric surfaces deny the adhesion of inks.
Solutions
Even powder application: The most perfect adhesion is from even powder application.
Correct curing settings: Calibrate your heat press to the proper temperature and time.
Using high-quality materials: This includes using high-quality DTF ink and powder
Proper fabric preparation: Properly pre-treating the fabric enhances the bonding of the inks.
2. White Ink Issues
Problem: White ink coverage tends to be patchy or incomplete. Several factors contribute to this, including wrong settings, printhead clogging, and poor ink.
Causes
- Wrong Setting: Wrong white ink density settings lead to undesirable prints.
- Clogged Printheads: Sometimes, white ink is blocked and unable to circulate smoothly, thus providing uneven coverage.
- Poor Ink: Poor white ink has reduced opacity and will result in poor performance.
Solutions
Optimize Settings: The proper white ink density calls for optimizing your printer settings.
Clean Printheads: Cleaning the printheads from time to time will help avoid clogging and allow the smooth flow of ink.
Use High-Quality Ink: For the best output, white ink should be of high quality and made especially for DTF printing.Â
3. Color Mismatch
Problem: The printed colors can appear washed out, dulled, or significantly different from the original design. There can be a variety of causes, such as incorrect color profiles, poorly calibrated printers, and inconsistent ink quality.
Causes
- Incorrect Color Profiles: Mismatched color profiles between your design software, printer, and monitor result in significant color deviations.
- Poorly Calibrated Printer: A printer that needs to be calibrated can produce consistent and accurate colors.
- Inconsistent Quality of Ink: This sometimes leads to color inconsistency and inaccuracy.
Solutions
- Create Accurate Color Profiles: Develop specific color profiles for your printer and ink combination to ensure accurate color reproduction.
- Calibrate Your Printer: Calibrate your printer occasionally to achieve consistency in the color.
- Use Consistent, High-Quality Ink: Use consistent ink and avoid color variations using high-quality ink.
4. Cracking and Peeling
Problem: The prints are mostly cracking or breaking off the material, especially when washed. Some contributing factors to this include improper curing time or temperatures, impure ink powders, and fabric prep.
Causes
- Inadequate curing: The ink will have inadequate adhesion if the cure part cannot provide heat.
- Poor-Quality Materials: Materials with poor-quality DTF inks require more excellent toughness and adhesive force.
- Improper Fabric Preparation: If the pre-treatment is adequate or proper, it may enhance the ink's adhesion to the fabric.
Solutions
- Optimize the Curing Process: Increase curing time and temperature to ensure the ink adheres appropriately.
- Use Quality Materials: Use premium DTF inks and powders to last long and stick on well.
- Proper Fabric Preparation: Pre-treat the fabric properly to ensure it can be receptive to the ink.
5. Image Distortion
Problem: The printed image needs to be more balanced from its intended original design. It can be stretched, compressed, and slanted in various ways. The result will be a bad visual presentation that does not depict the form of the image as designed.
Causes
- Printing Setting Errors: The wrong resolutions or print modes may cause images to be distorted.
- Low-Quality DTF Film: Low-quality film stretches or shrinks the image during transfer.
- Incorrect Transfer Process: If the heat press settings, pressure, or time are incorrect, the image will distort.
Solutions
- Printer Settings: Check whether your printer settings, resolution, and print mode are correct. You can check the specific recommendations in the printer's manual.
- High-Quality Film: You can invest in high-quality DTF film to reduce the distortion of images.
- Follow the Recommended Transfer Process: Adhere to the recommended heat press settings, pressure, and time to ensure proper transfer and avoid distortion.
6. Uneven Application of Powder
Problem: The print section will create many problems because of uneven powder dispersion. For example, a print could look spotted and blotchy because the ink can't stick evenly on parts of it; the problem is in the process, as some parts of the even and uneven powder distribution have defects. It may be spotted and speckled when making prints somewhere else.
Causes
- Faulty Powder Shaker: Sometimes, it doesn't work efficiently, and that's probably because it was not made good; thus, it won't distribute the powder accordingly.
- Inadequate Powdering Method: The powdering method can lead to uneven distribution, either because of an inconsistent shake or poor coverage.
- Low-quality powder: This could result in inadequate adhesion and poor flow properties.
Solutions
Shaker Maintenance and Cleaning: Maintain your powder shaker regularly for proper functioning.
Application Technique: Practice uniformly when powdering prints for proper and even coverage.
Use High-Quality Powder: Invest in the highest-quality DTF powder. It is designed to give the best adhesion and even distribution.
7. Ink Bleeding
Problem: The printed design bleeds into the surrounding fabric, becoming blurred, smeared, or hazy. The ink spreads outside of the intended design area, ruining the overall look and quality of the garment.
Causes
- Overload in the Print Head: Applying too much ink will create a pool and bleed.
- Incorrect Curing: Incorrect curing temperature or time would lead to inappropriate ink settings, which would cause the ink to bleed out.
- Low-quality materials: For example, using low-quality DTF ink or powder may result in low colorfastness and bleeding.
- Failure to prepare the fabric correctly: Poor pre-treatment could affect ink adhesion and lead to bleeding.
Solutions
- Optimize Ink Settings: Modify your printer settings to limit ink application without losing image quality.
- Calibrate the Curing Process: You must calibrate your oven to the appropriate temperature and time for your particular ink and fabric combination.
- Suitable Quality Materials: To make the prints look better and last longer, spend money on quality DTF inks, powders, and pre-treatment solutions.
- Proper Pre-Treatment: Treat your fabric right to increase the adhesion of the ink and avoid bleeding.
Some Tips for a Successful DTF Transfer
Take your DTF print to the next level with these advanced tips from Picasso DTF Print. Implementing the above best practices will result in consistent, high-quality outcomes.
- Equipment Regular Upkeep: For best prints, keep your printer and heat press clean, as well as others.
- Quality Materials: Utilize the best materials, such as DTF ink, transfer film, and substrates.
- Experiment and Fine-tune: Experiment with different settings to optimize your project's perfect combination of settings.
- Stay Up to Date: Stay informed on any changes in DTF printing technology and technological advancement.
Following these tips, coupled with a sense of the most common mistakes one would face when DTF printing transfers, will lead a person to the best achievable result, and one's DTF printing projects will reach heights never before reached.
Final Thoughts
As explained in this blog post, understanding the most common DTF transfer errors and taking steps can significantly improve your DTF prints. As the saying goes, practice and experiment to master the art of DTF printing.
For premium DTF printing services, you need not look elsewhere. Picasso DTF Print is here to rescue, offering a high-quality printing service using cutting-edge technology and superior materials.
Contact us today to discuss your DTF printing needs, and let us make your designs a reality.
0 comments